在电缆制造行业中,设备的高效运转直接关系到生产效率和产品质量。电缆绕包机作为生产线上的核心设备之一,其稳定性和寿命往往取决于日常维护的精细程度。据统计,因保养不当导致的设备故障占停机事故的60%以上。如何制定一套科学、全面的电缆绕包机保养计划?本文将深入解析从日常清洁到系统性检修的七大核心维度,帮助企业实现设备全生命周期管理。
一、日常维护:设备稳定运行的“基本功”
日常维护是保养计划的基础环节,通过简单的操作即可显著降低突发故障率。操作人员需每日完成以下任务:
- 表面清洁:使用无纺布或软毛刷清除绕包机表面的粉尘、油污,避免杂质进入传动部件;
- 润滑点检查:确认导轨、齿轮、轴承等关键部位的润滑状态,及时补充专用润滑脂;
- 紧固件排查:检查螺丝、螺母是否松动,特别是绕包头、张力控制模块的固定部件;
- 运行参数记录:记录设备电流、温度、噪音等数据,建立异常波动的预警机制。
二、定期检查:预防性维护的核心策略
根据设备使用频率制定周检、月检、季检三级检查体系:
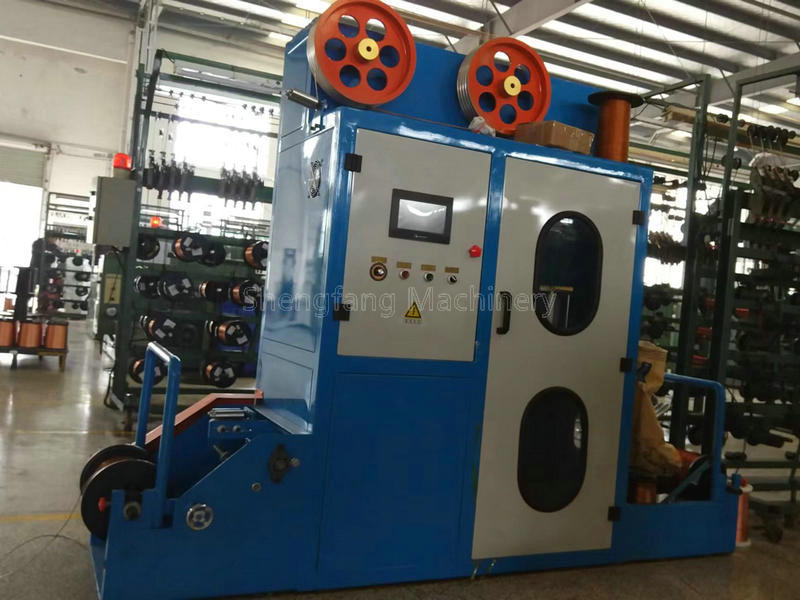
- 周检重点:检测绕包带的张力均匀性,校准纠偏装置精度,检查气动元件的气密性;
- 月检项目:拆解清理绕包模具,测量传动皮带磨损量,评估伺服电机的碳刷寿命;
- 季检深度维护:对主轴轴承进行超声波探伤,校验PLC控制系统逻辑,更新老化线路。
三、润滑管理:降低磨损的关键环节
润滑不当是导致机械故障的常见原因。建议采用“三定原则”:
- 定点:明确设备说明书标注的32个标准润滑点(如摆线针轮、滑轨滑块);
- 定质:选用耐高温、抗氧化的合成润滑脂,避免不同型号油脂混用;
- 定量:通过注油枪精准控制注入量,过量润滑可能引发散热问题。
四、易损件更换计划:成本与效能的平衡术
建立易损件生命周期档案,可减少非计划停机:
- 绕包模具:每生产800-1000公里电缆后需翻新或更换;
- 同步带:建议每12个月强制更换,高负荷工况下缩短至8个月;
- 轴承组件:通过振动监测判断状态,累计运行6000小时后需拆卸保养。
五、操作规范培训:从源头减少人为损伤
调查显示,30%的设备故障源于操作失误。保养计划需包含:
- 岗前培训:新员工必须掌握急停按钮位置、过载保护机制等安全操作规范;
- 技能提升:每季度开展绕包角度调节、张力参数优化等专题培训;
- 考核机制:将设备点检完成度纳入绩效考核,强化责任意识。
六、数字化记录与分析:智能运维新趋势
引入设备管理软件(如EAM系统)可实现:
- 电子台账:自动记录保养时间、耗材批次、故障代码;
- 数据分析:通过历史数据预测轴承失效周期,优化备件采购计划;
- 远程监控:利用物联网传感器实时传输振动、温度数据,提前预警潜在风险。
七、环境适配性优化:延长设备寿命的隐性要素
电缆绕包机对运行环境有严格要求,需重点关注:
- 温湿度控制:保持车间温度在15-30℃、湿度≤70%,防止电气元件受潮;
- 粉尘防护:在绕包区域加装集尘装置,避免金属碎屑进入精密部件;
- 地基减震:对高频振动的机型配置橡胶减震垫,降低共振对结构件的损伤。
通过上述七大维度的系统化保养,企业可将电缆绕包机的综合故障率降低40%以上。某知名线缆企业实施该方案后,设备平均无故障时间(MTBF)从1200小时提升至2100小时,年度维护成本下降18%。这印证了科学的保养计划不仅是设备管理工具,更是企业降本增效的战略性投资。
TAG: