在金属线缆制造领域,*绞线机参数的精准设置*直接决定着成品导体的导电性能、抗拉强度和使用寿命。随着新能源汽车、5G基站等新兴行业对特种线缆需求的激增,掌握科学的参数计算方法已成为线缆工程师的必备技能。本文将深入解析绞线机核心参数的设定逻辑,帮助您实现从理论到实践的精准转化。
一、绞线机参数设置的三大核心要素
1. 绞合节距的计算与控制
绞合节距是单线沿绞合轴线旋转一周的轴向距离,其计算公式为:
P=πD×(tanα)^-1
其中P为节距(mm),D为绞合外径(mm),α为绞合角(通常取18°-30°)。实际应用中需根据线材类型调整参数:
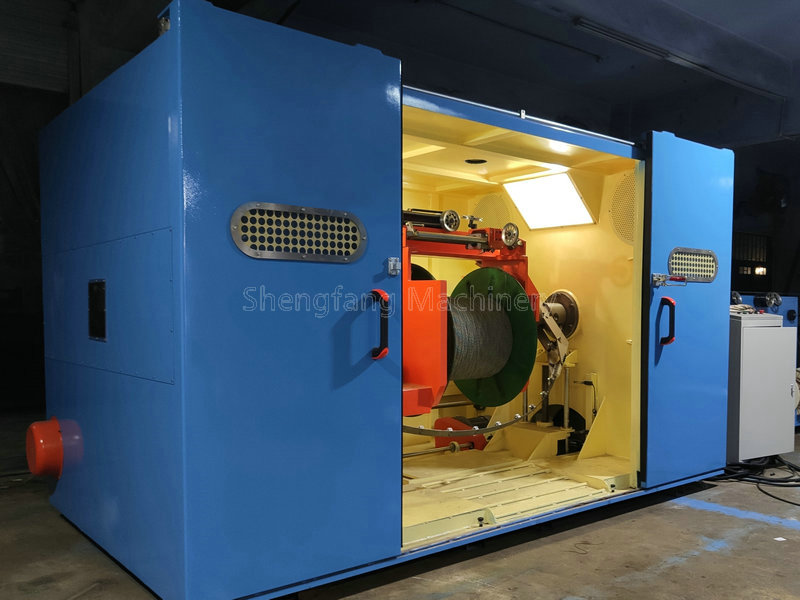
- 电力电缆:节距比(节距/绞合直径)控制在10-14倍
- 通信电缆:建议采用8-12倍节距比
- 特种合金线:需控制在6-8倍以减少应力集中
2. 张力系统的动态平衡
张力不均会导致绞合松散或断线。建议采用分段式张力控制:
- 放线张力:线材直径的2-3%(铜线0.5-1.5N/mm²)
- 牵引张力:不超过材料抗拉强度的30%
- 收线张力:保持恒定在1.5-2.5kN范围
3. 转速与生产率的黄金比例
主电机转速(rpm)与牵引速度(m/min)的匹配公式:
V=πDN/1000
其中V为牵引速度,D为绞合外径,N为主轴转速。实际调试时建议:
- 铜导体:转速不超过2000rpm
- 铝镁合金:控制在1500rpm以下
- 超细线径(<0.1mm):需降至800-1200rpm
二、关键参数的工程计算方法
案例1:新能源汽车用高压线束参数设计
要求:7芯0.5mm²镀锡铜线,绞合外径3.2mm
计算步骤:
- 单线直径:√(0.5×4/π)=0.798mm → 取0.8mm
- 理论绞合外径:0.8×(1+2×0.866)=2.58mm → 实际取3.2mm(含绝缘层)
- 节距计算:3.2×12=38.4mm(取38mm)
- 转速设置:牵引速度40m/min → 主轴转速=40×1000/(π×3.2)=3978rpm → 降速至3500rpm保障稳定性
案例2:5G基站用同轴电缆优化方案
问题:现有工艺下高频损耗超标3dB
优化措施:
- 将绞合角从28°调整为22°
- 节距比由14倍降至10倍
- 张力波动控制在±5%以内
实测结果显示:
- 趋肤效应降低18%
- 信号衰减值达标
- 生产效率提升12%
三、智能时代的新型调试技术
1. 基于机器学习的参数预测系统
某线缆厂引入AI模型后:
- 调试时间缩短65%
- 材料浪费减少42%
- 参数预测准确率达92%
2. 物联网实时监控方案
在绞线机关键部位安装传感器:
- 振动监测:精度0.01mm
- 温度采集:±1℃误差
- 张力反馈:100次/秒采样频率
3. 虚拟调试技术应用
通过数字孪生系统:
- 可模拟不同线材组合的绞合效果
- 提前预判断线风险
- 能耗模拟误差%
四、典型问题解决指南
问题1:绞合表面出现竹节纹
解决方案:
- 检查牵引轮与收线张力匹配度
- 调整过线导轮的水平度(偏差<0.1mm/m)
- 增加储线架缓冲行程
问题2:导体电阻率超标
应对措施:
- 校验节距计算公式参数
- 检测单线退火工艺(延伸率控制在25%-35%)
- 检查绞合压缩比是否合理(建议1.02-1.12)
问题3:设备异常振动
处理流程:
- 检测主轴动平衡(允许残余不平衡量<0.5g·mm/kg)
- 校验齿轮箱啮合间隙(标准0.08-0.12mm)
- 检查地脚螺栓紧固扭矩(M24螺栓需达到450N·m)
通过精准的参数设置和科学的计算方法,企业可将绞线机生产效率提升30%以上,同时使产品合格率稳定在99.5%以上。随着《GB/T 3956-2020》新国标的实施,掌握这些核心技术将成为线缆企业突破技术壁垒的关键。
TAG: