在5G基站、新能源汽车线束、工业自动化设备等领域,高品质绞合线缆已成为电力传输与信号稳定的核心载体。作为线缆制造的核心设备,绞线机的参数设置直接决定了导体的绞合均匀性、抗拉强度及电气性能。据统计,超过65%的线缆品质问题源于不合理的设备参数配置。本文将深入解析绞线机关键参数的设置逻辑,为生产人员提供可落地的优化方案。
一、张力控制:绞合品质的”隐形守护者”
绞线张力是参数设置的首要环节,直接影响导体延伸率与表面光洁度。当张力值低于材料屈服强度的30%时,容易出现绞距不均;超过50%则会导致铜丝拉伸变形。建议采用分段式张力控制:
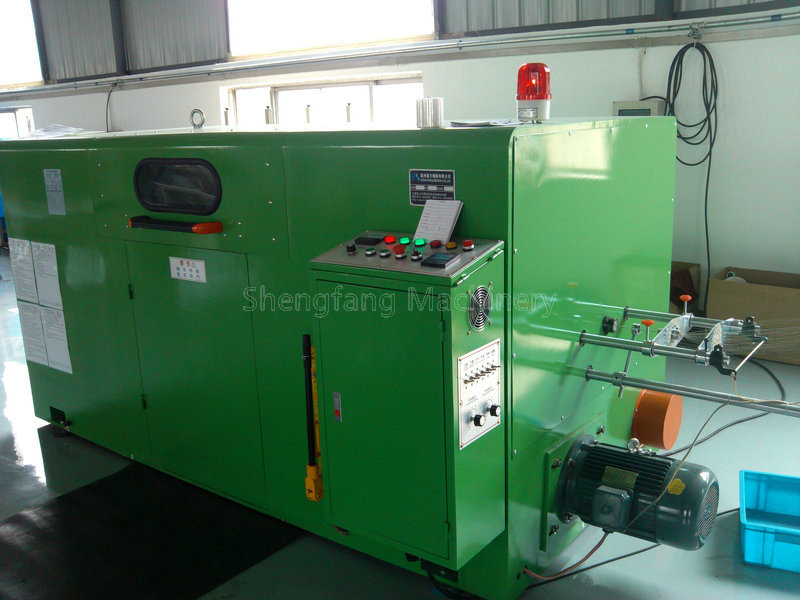
- 放线环节:设置初始张力为材料抗拉强度的15%-20%
- 绞合环节:通过PID算法动态调节张力波动,保持±3%的稳定性
- 收线环节:施加5%-8%的反向张力消除残余应力
某新能源车企的线束车间实践表明,张力标准差从0.8N降至0.3N后,绞合导体的直流电阻波动率下降了42%。
二、绞距与节距比:决定电气性能的关键参数
理论绞距计算公式:P=π×(D+d)/tanθ(D为绞合外径,d为单丝直径,θ为绞合角)。实际生产中需考虑以下修正因素:
- 导体材质(铜/铝的延伸系数差异达1.68倍)
- 绝缘层厚度(每增加0.1mm需补偿2%-3%绞距)
- 绞合方向(S向绞合比Z向需增加5%-8%节距)
案例对比:某通信电缆厂将7芯导体的节距比从12:1优化至14:1后:
- 高频信号衰减降低18dB/km
- 弯曲疲劳寿命提升至15000次循环
- 生产速度提高22%且能耗下降15%
三、转速与收线速度的动态平衡
建立绞笼转速(n)与收线速度(v)的数学模型:v=π×D×n×cosα(α为绞合角)。实际操作中需重点关注:
- 线速度差控制:收线速度应比理论值快0.5%-1.2%,避免松股
- 分层绞合设备需设置差速补偿系数(每增加一层补偿3%-5%)
- 变频器加速时间建议设置为2-3秒,防止急启急停造成跳股
某军工线缆企业通过引入自适应速度控制系统,成功将不同规格导体的换型时间从45分钟缩短至8分钟,同时将断线率控制在0.03次/万米以内。
四、温度与润滑的协同控制
现代高速绞线机(≥2000rpm)必须建立温度补偿机制:
- 每升高10℃需调整:
- 绞合角减小0.5°-0.8°
- 张力降低4%-6%
- 润滑剂流量增加15-20ml/min
- 在线测温系统应安装在距绞合点30-50cm位置
- 纳米级润滑剂建议采用雾化喷射,覆盖率达到85%以上
某特种电缆厂的实测数据显示,将工作温度稳定在35±2℃区间后:
- 铜导体表面划伤率下降76%
- 润滑油消耗量减少40%
- 设备连续工作时间延长3.2倍
五、智能化参数管理系统构建
先进企业已开始部署参数自学习系统,其运行逻辑包括:
- 建立包含5000+组工艺参数的数据库
- 通过机器学习算法匹配材料特性与设备状态
- 实时监测8-12项质量指标并动态修正参数
- 生成三维工艺窗口图指导优化方向
某上市公司引入智能系统后,新产品开发周期缩短58%,不良品成本下降至0.12%,年度综合效益提升2300万元。
TAG: